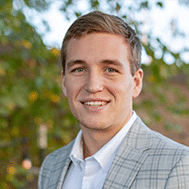
Engineer and Government Technology Consultant Specialist
InterLocking Metasurfaces (ILMs) are arrays of patterned surface features that enable joining adjacent bodies in various materials. The geometry of the surface topology depends on the desired material properties. The adjoining surfaces can then “snap” together to create structural joints with extremely high mechanical strength. Similar to Legos, the surfaces can be attached or detached quickly and easily. The orientation of the connection can be configured in any manner and optimized for all types of loads (tensile, shear, torque, etc). ILMs are advanced alternatives for traditional fastening methods like bolts, welding, adhesives, etc.
Initially invented in a Department of Energy (DOE) Lab as an advanced solution for a high-tech problem, ILMs are now being commercialized to benefit all sectors of industry. If you have an existing engineering challenge that involves attaching parts together, please contact us to explore if ILMs can improve your product, reduce costs, and increase operational efficiency.
We are currently in development of both the Generative Design Software and the Established Manufacturing Process to reliably fabricate ILMs into a deliverable product. If you have any interest in collaborating, via technical expertise or investment, we would love to connect. Our venture was initiated from the DOE Emerging Tech Studio, enabled by the National Nuclear Security Administration (NNSA) and the U.S. Department of Energy (DOE) Office of Technology Transitions (OTT), in conjunction with FedTech’s Boost program.
The performance of ILMs can be tailored to meet specific needs by adjusting factors such as unit cell size, topology, and placement.
Unlike most other fastening methods,
Due to a synergistic stiffening and strengthening effect, the effective strength of a 1×11 ILM array was four times higher than that of 11 independent 1×1 unit cells
Originally designed as a creative solution to a high-tech problem, the advantages of ILMs shine best in similar environments where the complexity of the product cannot be constrained to the fall backs of traditional fastening methods.
ILMs can also serve as a phenomenal solution to even the simplest engineering challenges. Ranging from defense, aerospace, and micro-robotics to civil construction and consumer products, ILMs can be useful anytime two things need to be attached together.
Engineer and Government Technology Consultant Specialist
Materials Engineering, MBA, and Experienced Founder
Ex Lockheed Martin Aerospace Engineer and SMB Operator